La scelta del trattamento superficiale è un problema che ogni designer deve affrontare. Esistono molti tipi di opzioni di trattamento superficiale e un designer di alto livello non dovrebbe solo considerare l'economia e la praticità del design, ma prestare attenzione al processo di assemblaggio e persino ai requisiti ambientali. Di seguito è riportata una breve introduzione ad alcuni rivestimenti comunemente usati per i dispositivi di fissaggio in base ai principi di cui sopra, come riferimento da parte dei professionisti della chiusura.
1. Elettrogalvanizzazione
Lo zinco è il rivestimento più comunemente usato per gli elementi di fissaggio commerciale. Il prezzo è relativamente economico e l'aspetto è buono. I colori comuni includono il verde nero e militare. Tuttavia, la sua prestazione anticorrosiva è media e la sua prestazione anticorrosiva è la più bassa tra gli strati di placcatura di zinco (rivestimento). Generalmente, il test di spruzzatura salina neutra di acciaio zincato viene effettuato entro 72 ore e vengono utilizzati anche agenti di tenuta speciali per garantire che il test di spruzzatura salina neutra dura più di 200 ore. Tuttavia, il prezzo è costoso, che è 5-8 volte quello dell'acciaio zincato normale.
Il processo di elettrogalvanizzazione è soggetto a idrogeno ricchezza, quindi i bulloni al di sopra del grado 10.9 non sono generalmente trattati con zincatura. Sebbene l'idrogeno possa essere rimosso utilizzando un forno dopo la placcatura, il film di passivazione verrà danneggiato a temperature superiori a 60 ℃, quindi la rimozione dell'idrogeno deve essere effettuata dopo l'elettroplatura e prima della passione. Ciò ha scarsa operabilità e costi di elaborazione elevati. In realtà, gli impianti di produzione generale non rimuovono attivamente l'idrogeno se non obbligatoria da clienti specifici.
La coerenza tra la coppia e la forza di pre -serraggio dei dispositivi di fissaggio zincati è scarsa e instabile e generalmente non sono utilizzate per collegare parti importanti. Al fine di migliorare la coerenza del precarico della coppia, può anche essere utilizzato il metodo di rivestimento di lubrificazione dopo la placcatura per migliorare e migliorare la coerenza del precarico della coppia.
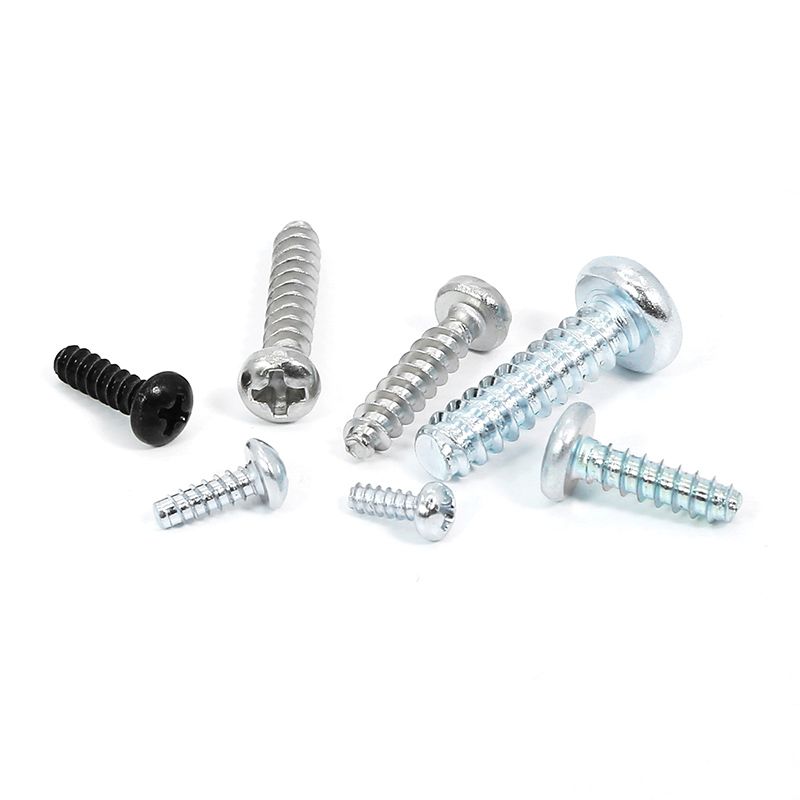
2. Fosfating
Un principio di base è che il fosfating è relativamente più economico della galvanizzazione, ma la sua resistenza alla corrosione è peggiore della zincatura. Dopo il fosfating, è necessario applicare l'olio e la sua resistenza alla corrosione è strettamente correlata alle prestazioni dell'olio applicato. Ad esempio, dopo la fosfatazione, applicando un olio antiruggine generale e conducendo un test di spruzzatura salina neutra per soli 10-20 ore. L'applicazione dell'olio antiruggine di alta qualità può richiedere fino a 72-96 ore. Ma il suo prezzo è 2-3 volte quello del petrolio di fosfazione generale.
Esistono due tipi di fosfating comunemente usati per chiusure, fosfating a base di zinco e fosfating a base di manganese. Il fosfating a base di zinco ha una migliore prestazione di lubrificazione rispetto al fosfating a base di manganese e il fosfating a base di manganese ha una migliore resistenza alla corrosione e resistenza all'usura rispetto alla placcatura di zinco. Può essere usato a temperature che vanno da 225 a 400 gradi Fahrenheit (107-204 ℃). Soprattutto per la connessione di alcuni componenti importanti. Come bulloni di asta di collegamento e dadi del motore, testata, cuscinetto principale, bulloni del volano, bulloni e dadi delle ruote, ecc.
I bulloni ad alta resistenza utilizzano fosfating, che possono anche evitare problemi di abbraccizzazione idrogeno. Pertanto, i bulloni superiori al grado 10.9 nel campo industriale utilizzano generalmente il trattamento della superficie fosfating.
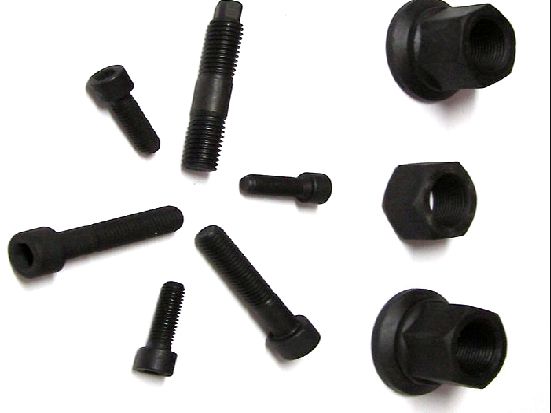
3. Ossidazione (annuo)
Blackening+Oiling è un rivestimento popolare per gli elementi di fissaggio industriali perché è il più economico e sembra buono prima del consumo di carburante. A causa del suo anneri, non ha quasi alcuna capacità di prevenzione della ruggine, quindi arrugginirà rapidamente senza olio. Anche in presenza di olio, il test di spruzzatura salina può durare solo per 3-5 ore.
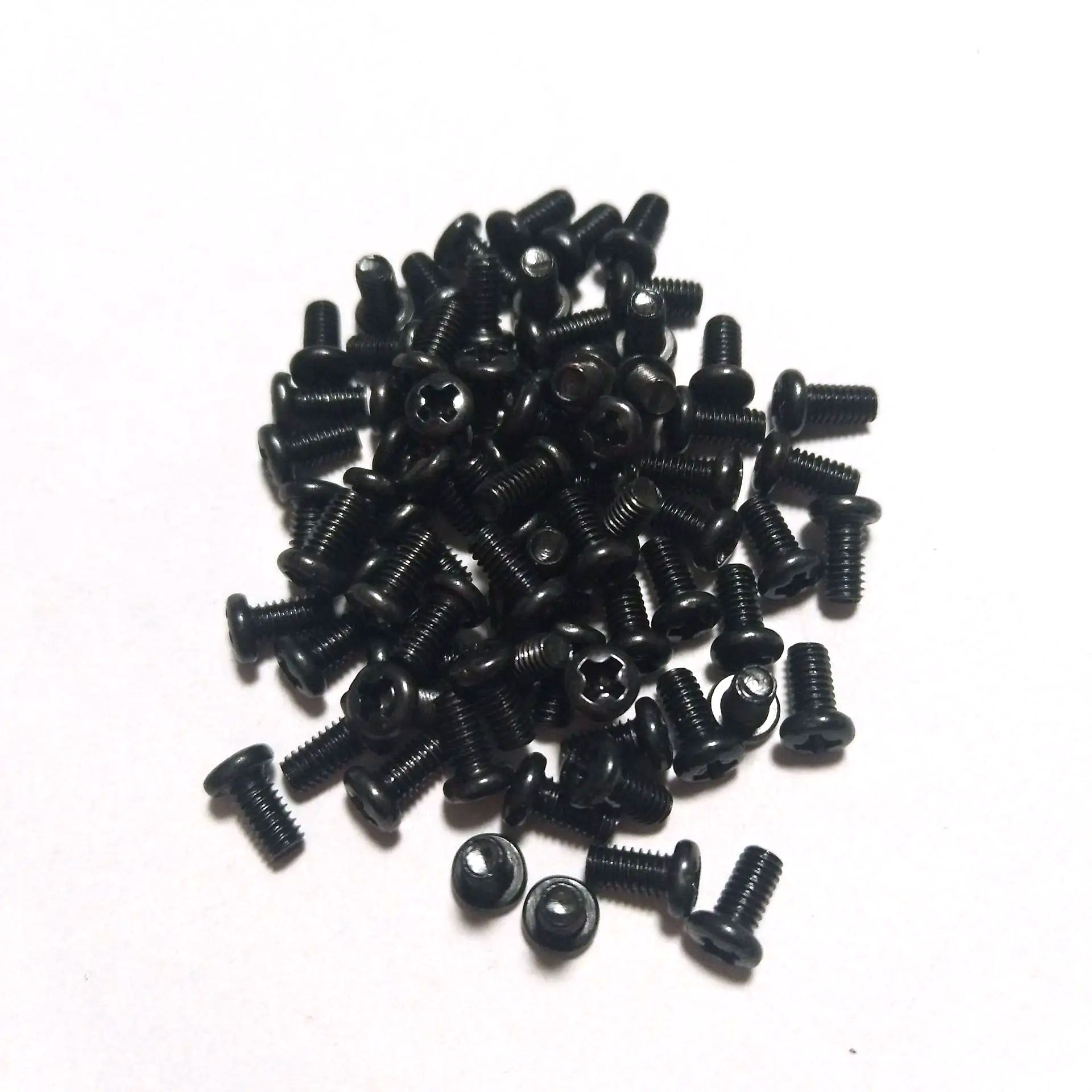
4. Partizione elettroplante
La placcatura del cadmio ha un'eccellente resistenza alla corrosione, specialmente negli ambienti atmosferici marini, rispetto ad altri trattamenti superficiali. Il costo del trattamento liquido dei rifiuti nel processo di cadmio elettroplante è elevato e il suo prezzo è di circa 15-20 volte quello dello zinco elettroplativo. Quindi non viene utilizzato nelle industrie generali, solo per ambienti specifici. Fissaggi utilizzati per piattaforme di perforazione petrolifera e aerei HNA.
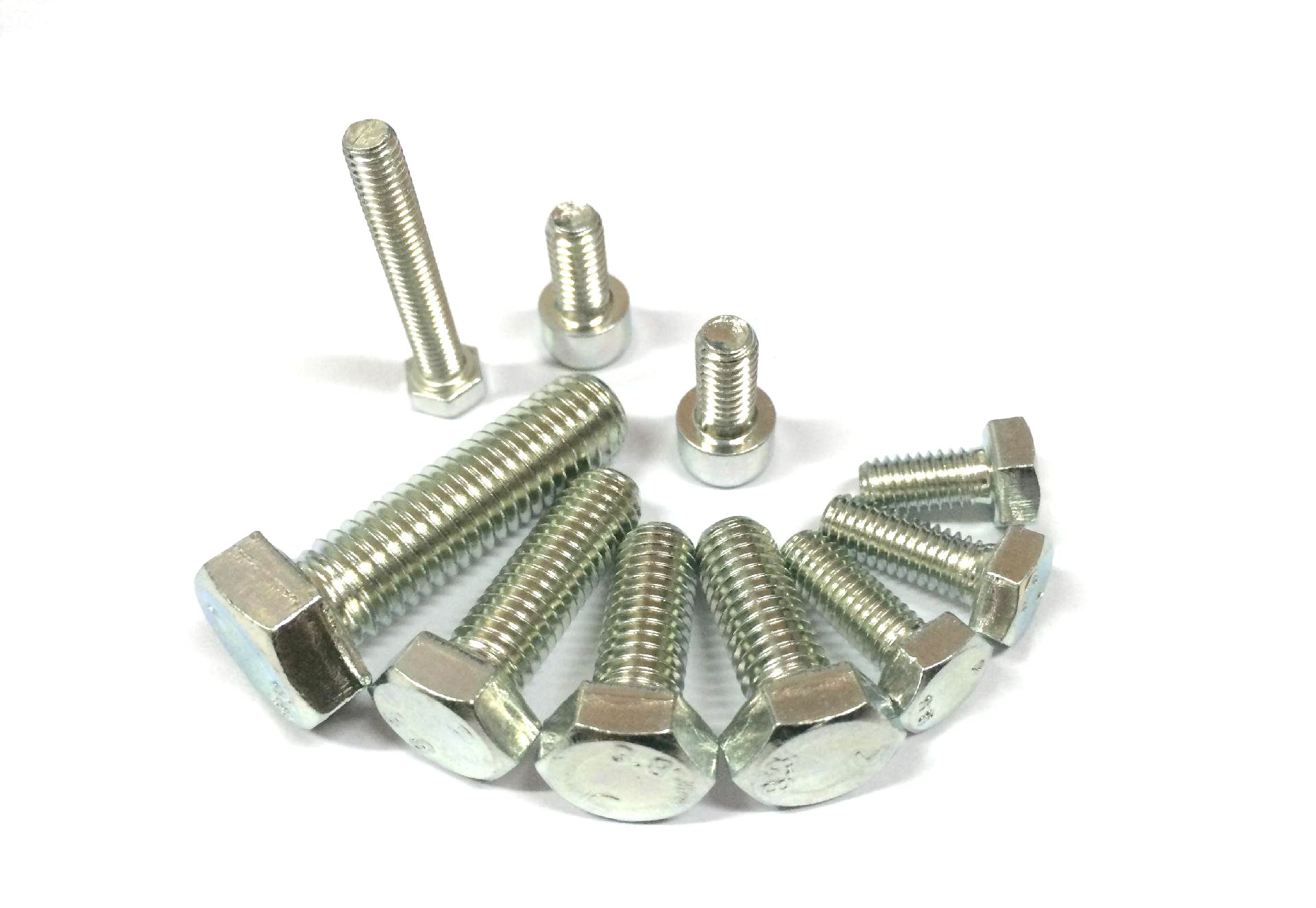
5. Placting Chromium
Il rivestimento del cromo è molto stabile nell'atmosfera, non facile da cambiare colore e perdere lucentezza e ha un'alta durezza e una buona resistenza all'usura. L'uso della placcatura di cromo sui dispositivi di fissaggio è generalmente utilizzato per scopi decorativi. Raramente viene utilizzato in campi industriali con elevati requisiti di resistenza alla corrosione, poiché i buoni elementi di fissaggio cromati sono ugualmente costosi come in acciaio inossidabile. Solo quando la resistenza in acciaio inossidabile è insufficiente, vengono invece usati i dispositivi di fissaggio cromati.
Per prevenire la corrosione, il rame e il nichel devono essere placcati prima di cromo. Il rivestimento di cromo può resistere a temperature elevate di 1200 gradi Fahrenheit (650 ℃). Ma c'è anche un problema di idrogeno abbraccio, simile all'elettrogalvanizzazione.
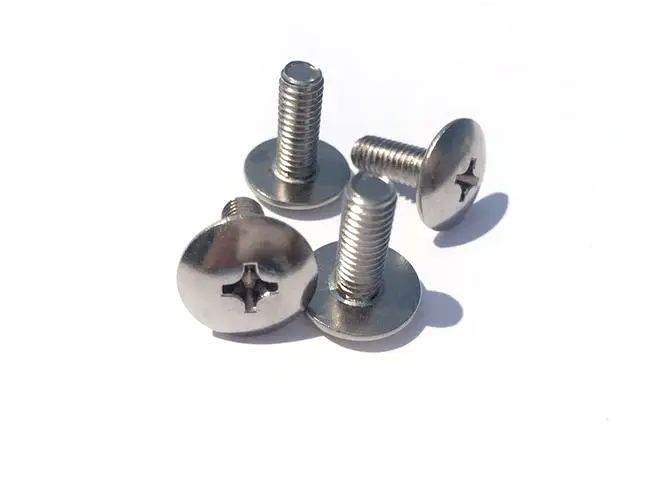
6. Nickel Plating
Utilizzato principalmente in aree che richiedono sia anticorrosione che buona conducibilità. Ad esempio, i terminali in uscita delle batterie del veicolo.
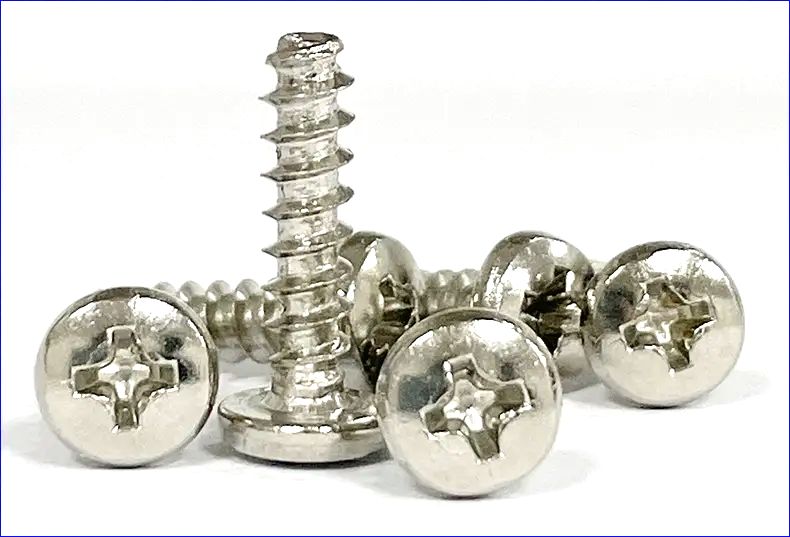
7. Galvanizzazione a caldo
La galvanizzazione a caldo è un rivestimento di diffusione termica di zinco riscaldato a un liquido. Lo spessore del rivestimento è compreso tra 15 e 100 μ m. E non è facile da controllare, ma ha una buona resistenza alla corrosione e viene spesso utilizzato in ingegneria. Durante il processo di galvanizzazione a caldo, c'è un grave inquinamento, inclusi i rifiuti di zinco e il vapore di zinco.
A causa del rivestimento spesso, ha causato difficoltà nell'avvio di filettature interne ed esterne nei dispositivi di fissaggio. A causa della temperatura dell'elaborazione galvanizzante a caldo, non può essere utilizzato per i dispositivi di fissaggio al di sopra del grado 10.9 (340 ~ 500 ℃).
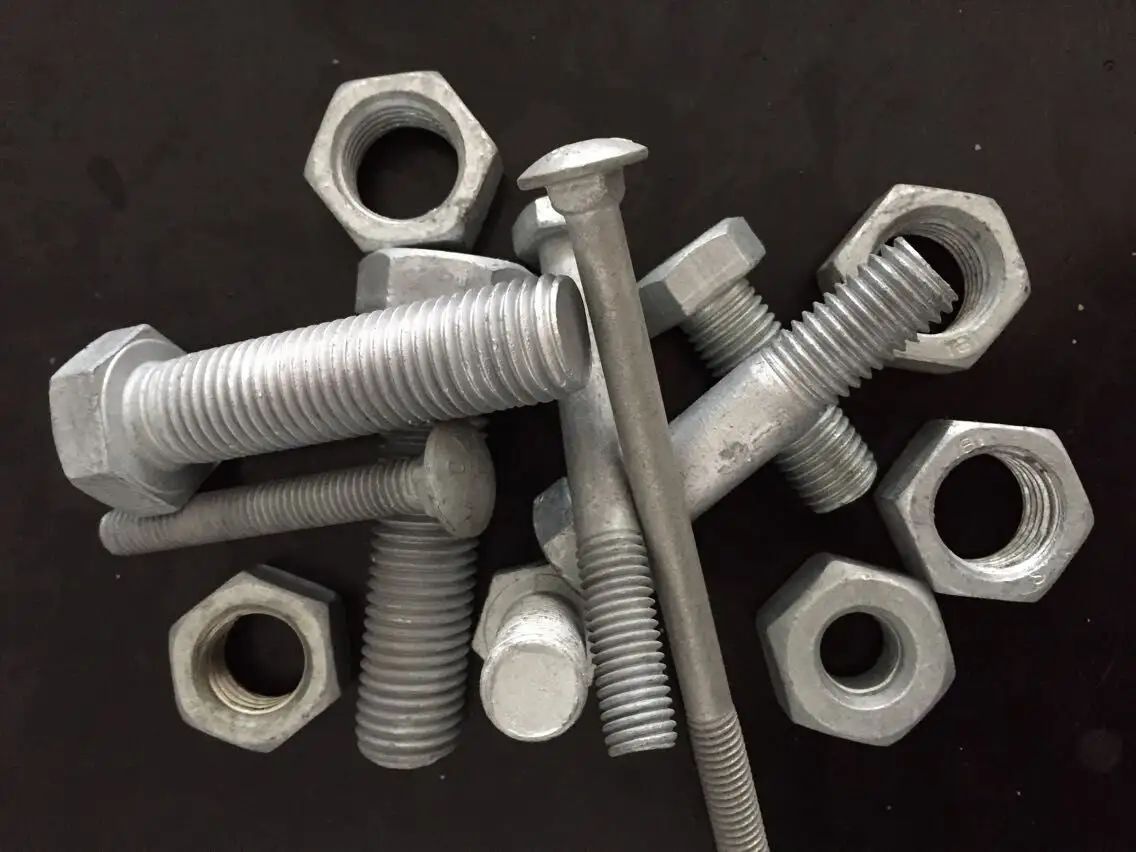
8. Infiltrazione di zinco
L'infiltrazione di zinco è un rivestimento di diffusione termica metallurgica solida della polvere di zinco. La sua uniformità è buona e uno strato uniforme può essere ottenuto in fili e buchi ciechi. Lo spessore della placcatura è di 10-110 μ m. E l'errore può essere controllato al 10%. La sua forza di legame e le prestazioni anticorrosiva con il substrato sono le migliori nei rivestimenti di zinco (come elettrogalvanizzazione, zincatura a caldo e dacromet). Il suo processo di elaborazione è privo di inquinamento e più ecologico.
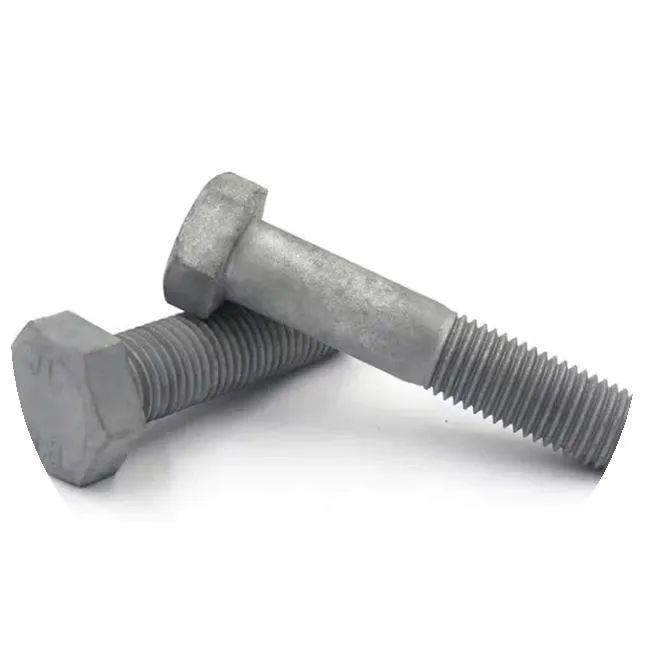
9. Dacromet
Non esiste un problema di abbracci per idrogeno e le prestazioni di coerenza del precarico della coppia sono molto buone. Senza considerare i problemi di cromo e ambientale, Dacromet è in realtà il più adatto per dispositivi di fissaggio ad alta resistenza con elevati requisiti anticorrosivi.
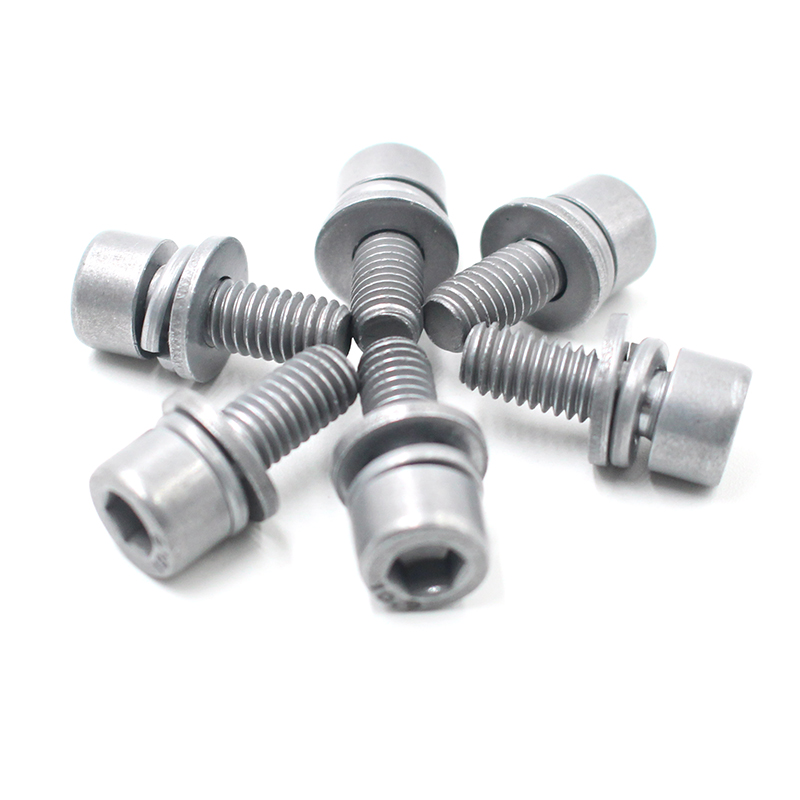
Tempo post: 19-19-2023